Research findings have shown that the leftover portions of biomass and waste can be used to produce an array of bioenergy. Though the purchase price of this bioenergy doesn’t seem to be currently competitive with petro-fuels and other forms of renewable energy. Continual and substantial efforts are being made to enhance techniques for conversion with the aim of decreasing manufacturing expenses.
In recent years, the thirst for in energy produced from biomass has declined because of an advancement in technology in which rendered fossil energy comparatively cheap. Nevertheless, the significant levels of greenhouse gas emissions, lethal air pollution, volatile fossil fuel costs, and the rapid increase in worldwide requirements for fuel for transportation have encouraged significant scientific endeavours in the advancement of bioenergy.
Bioenergy is the alternative form of energy directly obtained from biomass in different form of fuels based on the difference in the production processes. Biomass based energy sources are renewable resource, is being increasingly seen as a viable alternative fuel for the provision of sustainable energy in the future. Different types of biomasses have the potential to convert it into fuel like, bioethanol form biomass and biodiesel from algae.
The present review provides an in-depth overview of the technological details of the conversion techniques of biomass residues and waste to biofuels and bioelectricity. More specifically, the review presents a list of the waste-to-energy technological options. This article offers a comprehensive examination of the technical aspects involved in converting residues of biomass and waste into biofuels and bioelectricity.
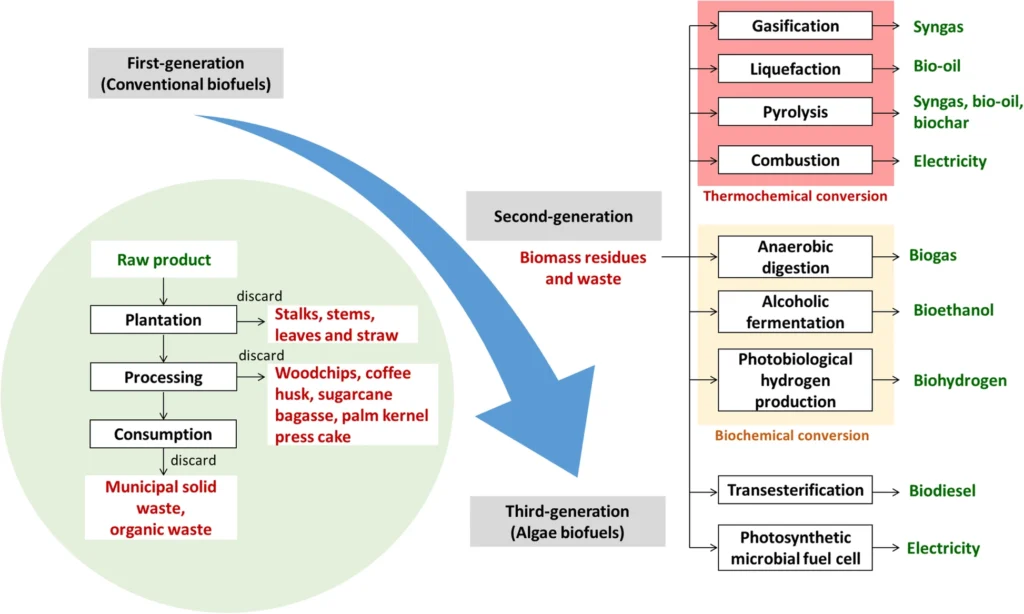
Figure 1. A schematic representation illustrating the progression of biofuel production, with a particular focus on second-generation biofuels derived from biomass residues and waste. These biofuels undergo various conversion processes to generate a diverse range of bioenergy. (Source: Lee, S.Y., Sankaran, R., Chew, K.W. et al. Waste to bioenergy: a review on the recent conversion technologies. BMC Energy 1, 4 (2019). https://doi.org/10.1186/s42500-019-0004-7)
- Thermochemical conversion
Thermochemical conversion is an approach that includes clevage and reconstructing chemical bonds in organic substances at high temperatures. This technique produces biochar (a solid material), synthesis gases, and oxygenated bio-oil. Thermochemical conversion encompasses three primary techniques: gasification, pyrolysis, and liquefaction. The choice of conversion method is often determined by factors such as the characteristics and amount of biomass feedstock, the desired form of energy, the context in which it will be used, concerns regarding the environment, affordability, and specific project requirements.
- Gasification
The process of gasification involves chemical reactions in an oxygen-deprived atmosphere. In order to generate flammable gas mixtures, this technique includes heating biomass at severe temperatures (500–1400 °C), ambient pressures up to 33 bar, and with little to no oxygen present. In the presence of a gasification agent and catalyst, the gasification process converts carbonaceous materials into syngas, which includes hydrogen, carbon monoxide, carbon dioxide, methane, higher hydrocarbons, and nitrogen. Many forms of energy and energy carriers, such as biofuel, hydrogen gas, biomethane gas, heat, power, and chemicals, are produced by using this syngas.
- Liquefaction
Two methods of converting biomass into bio-oil or biocrude are liquefaction and pyrolysis. The process of thermochemical liquefaction entails producing bio-oil in the presence of hydrogen at low temperatures and high pressures, either with or without a catalyst. Hydrothermal liquefaction (HTL), also known as hydrous pyrolysis, is a well-known liquefaction method that turns biomass into bio-oil by using subcritical water (SCW) at medium temperatures between 250 to 374 °C and working pressures between 40 and 220 bar. The HTL process includes gas production, solid deposit, dissolved chemicals in water, and breakdown and repolymerization reactions for bio-oil conversion. In the HTL process, high pressure helps to keep water in its liquid condition. However, when high pressure and temperature are combined, the dielectric constant and density fall, making hydrocarbons more soluble in water.
- Pyrolysis
Pyrolysis involves the breakdown of biomass through heat, without the presence of oxygen. The process typically occurs at temperatures between 350 and 550 °C, and can sometimes reach up to 700 °C. The pyrolysis process breaks down organic materials into a mixture of solids, liquids, and gases. Gasification and pyrolysis have distinct differences. In the case of gasification, it results in the production of fuel gas that can be effectively used for heat generation through combustion. Pyrolysis process generates a liquid fuel called pyrolysis oil, which can serve as a potential substitute for fuel oil in stationary heating or electricity generation applications. One benefit of the liquid fuel generated through pyrolysis, as opposed to the fuel gas from the gasification process, is that the resulting bio-oil can be easily stored and transported.
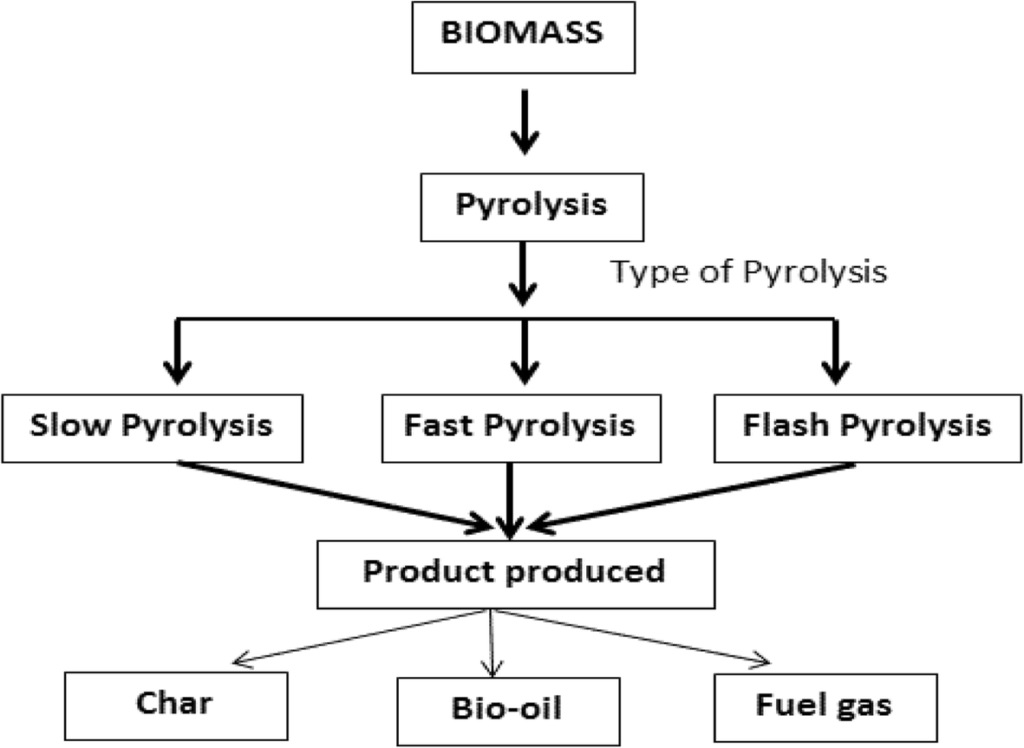
Figure 2. Illustration of different types of pyrolysis process (Source: Lee, S.Y., Sankaran, R., Chew, K.W. et al. Waste to bioenergy: a review on the recent conversion technologies. BMC Energy 1, 4 (2019). https://doi.org/10.1186/s42500-019-0004-7)
- Physical upgradation
Hot vapour filtration is a commonly used method in physical upgradation to improve the quality of bio-oil. It helps decrease the initial molecular weight of the oil and slows down the process of bio-oil ageing.
Hydrodeoxygenation upgradation
Another strategy, known as hydrotreatment or HDO, can provide increased oil yield, improved oil quality, and greater carbon recovery. This process requires the elimination of oxygen from oxygenated hydrocarbons through a catalytic reaction under high pressure (up to 200 bar), with a supply of hydrogen and moderate temperature (up to 400 °C). According to research, the HDO process has been found to enhance the quality of py-oil by improving oil stability and increasing energy density.
Biochemical conversion
Biochemical conversion involves the deployment of yeast along with bacteria to transform plant biomass or waste into valuable energy. The available process choices include anaerobic digestion, alcoholic fermentation, and photobiological methods, each resulting in the production of distinct biofuels.
Anaerobic digestion
Utilising the full potential of microalgae based biomass, which is rich in micronutrients including carbohydrates, proteins, and lipids, can enhance the financial, social, sustainability, and environmental benefits . An effective method to optimise nutrient extraction is through the anaerobic digestion acquired from the process of biodiesel synthesis. During anaerobic digestion, microorganisms transform the exhausted microalgae biomass into biogas, which mostly consists of methane (CH4) and carbon dioxide (CO2), along with small amounts of hydrogen sulphide (H2S). The energy content of the biogas corresponds to 20-40% of the lower heating value of the biomass. Anaerobic digestion may process wet material containing up to 90% moisture content. The anaerobic digestion process consists of three primary stages: hydrolysis, fermentation, and methanogenesis. Hydrolysis is a process that breaks down complex biomolecules in biomass into simpler biomolecules. Fermentation then utilises these basic biomolecules to produce volatile alcohols, acetic acid, fatty acids, as well as a mixture of H2 and CO2 gas. The gas combination was metabolised by methanogens, resulting in the production of biogas consisting of 60-70% CH4 and 30-40% CO2.
Alcoholic fermentation
Bioethanol is a fuel produced by the process of the fermentation of alcohol. This involves converting the fermentable sugars found in biomass residues, which are derived from the cellulose and hemicellulose components of biomass. This conversion takes place in the presence of yeast or bacteria. Microalgae species such as Chlorella, Chlamydomonas, Scenedesmus, Dunaliella, and Spirulina have been found to accumulate significant quantities of starch, glycogen, and cellulose, exceeding 50% of their dry weight. The raw ingredients required for bioethanol manufacturing are these intricate polysaccharides. Due to the microorganisms’ limited ability to metabolise the polysaccharides, hydrolysis is performed to enzymatically break down the polysaccharides into simpler sugars prior to its consumption. Acid/alkali and enzymes are the most frequently used hydrolysis procedures. The acid treatment is cost-effective and efficient, however, the acidic conditions may cause the sugars to undergo undesired transformations. On the other hand, enzyme based treatment is highly effective and does not produce unwanted by-products. However, enzymes are costly and operate at a slower pace. Prior to hydrolysis, cell disruption procedures can be employed to enhance the effectiveness and reduce the length of hydrolysis. The raw alcohol (10–15% ethanol) must be subjected to a concentration process employing distillation. The residual solid material can be further utilised through liquefaction, gasification, or microwave-assisted pyrolysis to produce valuable products.
Photobiological hydrogen production
Certain types of biomass, including microalgae, possess an inherent capacity to generate hydrogen gas when exposed to light. During the process of photosynthesis, microalgae convert water molecules into oxygen (O2) and hydrogen ions (H+). Hydrogenase enzymes catalyse the reduction of H+ ions to become H2 gas in the absence of oxygen. The oxygen produced during photosynthesis quickly hinders the hydrogenase enzymes and disrupts the release of hydrogen gas. Therefore, it is important to create an environment without oxygen in order to culture microalgae for the formation of H2 gas. There are two primary techniques for extracting photosynthetic hydrogen (H2) utilising microalgae. The initial method involves the concurrent generation of oxygen (O2) and hydrogen (H2) gas when exposed to light. Hydrogenase enzymes utilise electrons produced from the oxidation of water molecules to form H2 gas. In theory, this process has greater yields compared to the second strategy. However, the generation of H2 is quickly hindered by the formation of O2. An alternative method involves employing a two-phase system, wherein the initial phase involves cultivating microalgae under standard circumstances, followed by a second phase that stimulates ongoing production of H2 in an anaerobic and sulfur-deprived environment. Under conditions of sulphur deficiency, microalgae enter a survival mode in which they get the energy needed by the cells through the release of H2. In the two-phase system, the production of H2 would start to decrease after 60 hours of operation, and the highest possible yield of H2 might be as high as 198 kg H2 per hectare per day.
Transesterification
Transesterification is a chemical reaction in which fats and oils undergo conversion to produce esters and glycerol, facilitated by the presence of catalysts. The resulting fatty acid methyl ester (FAME) would possess similar physical properties to those of commercial petroleum fuel, while the by-product glycerol also holds commercial worth.
Biomass derived waste materials can be transformed into transportation fuels through the processes of transesterification, thermochemical conversion, and biochemical conversion. The selection of the procedure technology is contingent upon the type of final outcome and the available feedstocks. Thermochemical technology, which uses thermal heat, is generally less affected by the nature of biomass waste compared to biochemical systems for producing biofuels. However, the use of biomass waste for biofuel production is generally seen as more efficient in terms of material management, transportation, and conversion technology, as compared to biofuels derived from traditional edible food crops. However, ongoing research investigations are focused on addressing the shortcomings of current technologies and enhancing the efficiency and cost-effectiveness of the production methods used.
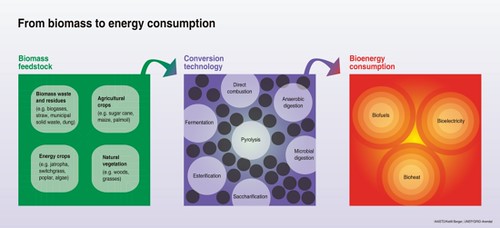
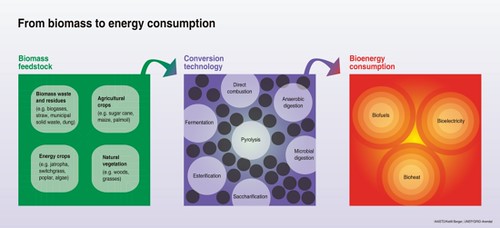
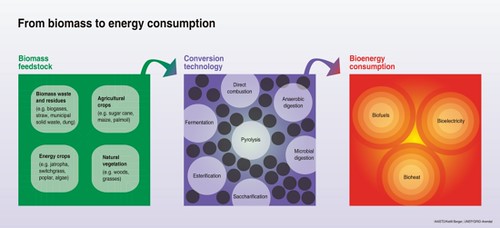
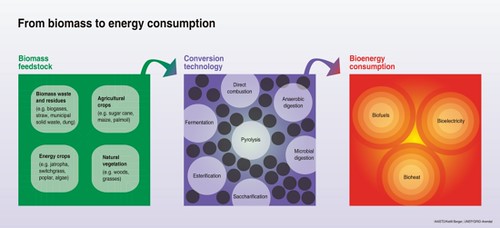
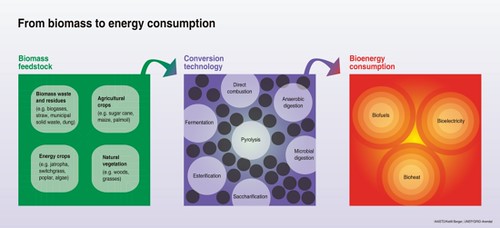
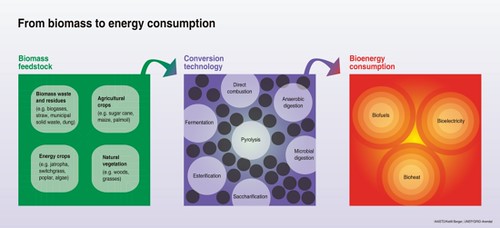
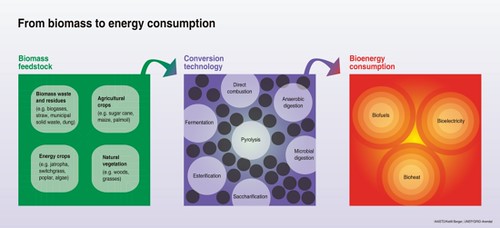
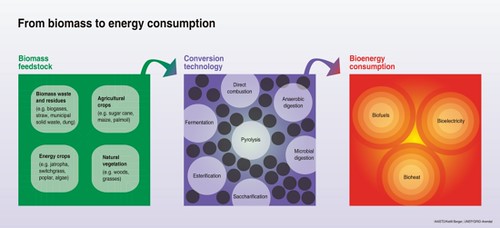
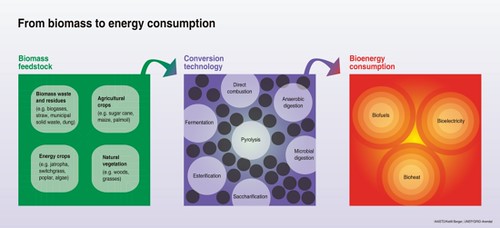
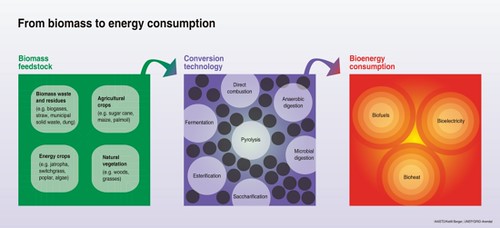
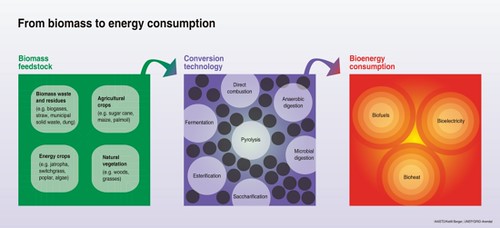
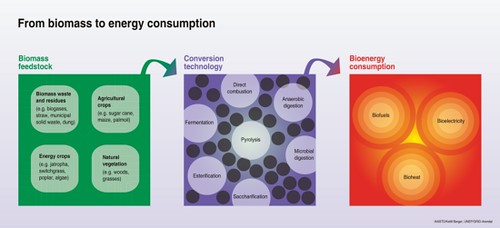
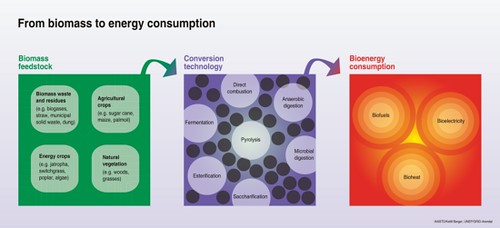
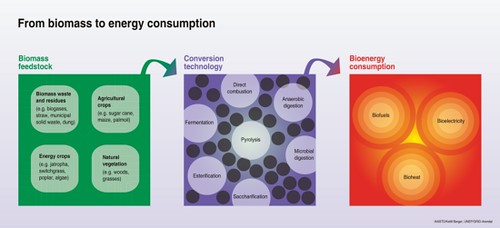
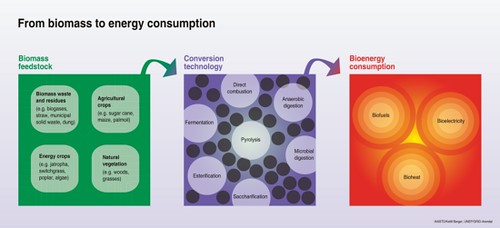
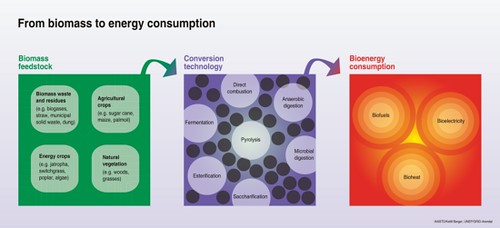
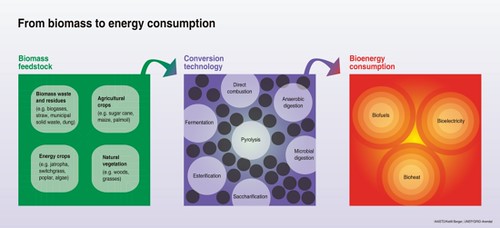
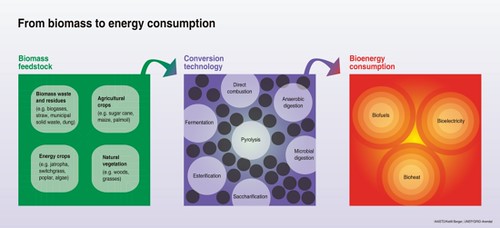
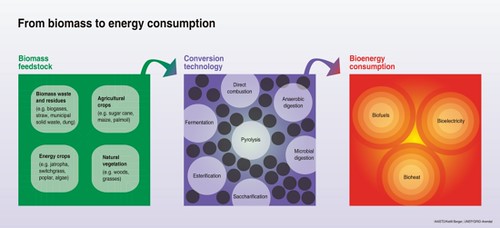
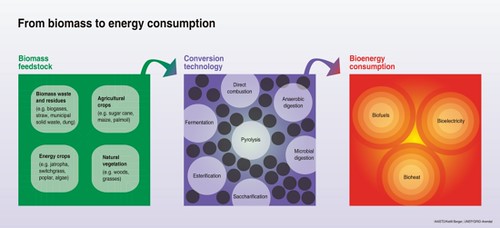